While they have roots dating back to the mid-1800s, over the last five decades, plastics have completely changed the way we live, work, and play. In fact, they have become an essential part of our lives. Although this material came from humble beginnings all those years ago, it has helped humanity accomplish unfathomable achievements, even playing a significant role in sending the first man to the moon, and so much more. After reviewing the infographic below on four uses of plastic, continue reading to learn more:
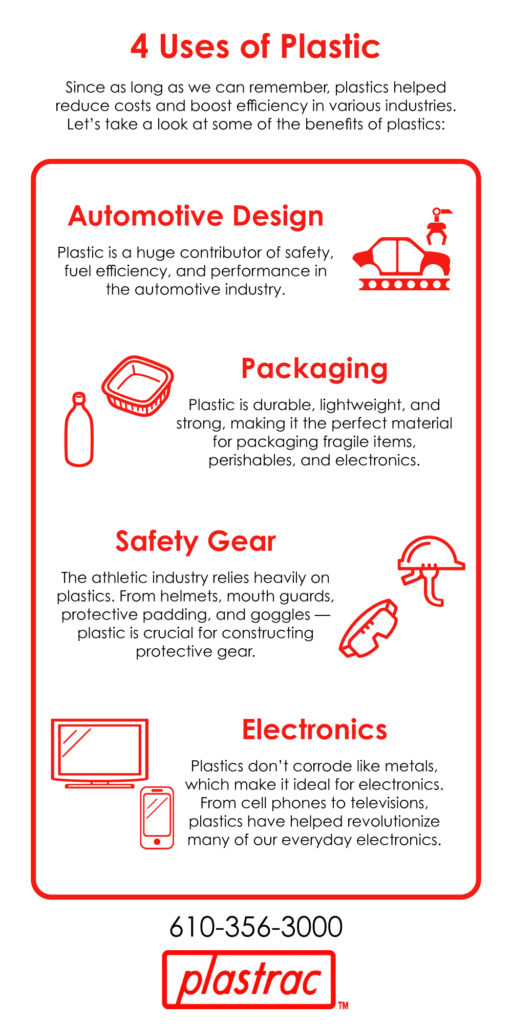
At Plastrac, our material blenders and loading systems have provided the plastics industry with efficient and dependable solutions for almost a quarter of a century. But we also have a true passion for plastics and their countless benefits. So, let’s take a look at the role plastics has played over the years — from a simple derivative of cotton fiber turned polymer almost 150 years ago, to the myriad uses in components from cars to spaceships, and everything in between.
What’s in a Word?
For centuries, the word “plastic” merely meant “bendable, easily shaped, or pliable.” In fact, it’s only recently (relatively speaking) that the term has become a name for a category of materials called polymers. In 1869, a gentleman by the name of John Wesley Hyatt was trying to find a substitute for ivory. During those times, the game of billiards was quickly growing in popularity, and it had begun to place a strain on the supply of natural ivory. Hyatt found that if he obtained cellulose, which was simply derived from cotton fibers, he could treat it with camphor and create a material that could be molded into a variety of shapes that could mimic natural substances such as horn, tortoiseshell, and yes…ivory.
A Far-Reaching Impact
To call this discovery revolutionary is an understatement of the greatest proportion. This breakthrough had far-reaching effects that would ripple throughout humanity for nearly the next century and a half, and counting. Back then, the discovery suddenly meant that productivity and manufacturing would no longer be limited by the constraints of nature. For instance, there was a finite supply of materials like wood, bone, horn, tusk, and ivory. But now, we humans could create our own materials, and would no longer be as reliant on those only found in nature.
And not only that, it was a boon to the environment as well. Plastics were hailed as the material that save the lives of innumerable tortoises, elephants, and other animals who were harvested for raw materials. Indeed, plastics were about to help the entire world and protect it from humanity’s increasing need for resources. And while these newly created materials called plastics were saving the earth from destruction, they also freed people from the social and economic limits that accompanied a scarcity of natural resources. All of this made wealth more attainable and widespread across the US and beyond.
And that was just the beginning.
In our next blog, we’ll take a look at the further development of plastics in the early 1900s and the continuation of the plastic revolution. For more information or to inquire about our line of gravimetric and volumetric blending equipment and material loaders, contact us today.